Przemysł 4.0 to termin odnoszący się do czwartej rewolucji przemysłowej, która wprowadza zaawansowane technologie do procesów produkcyjnych. Jego głównym celem jest zwiększenie efektywności, elastyczności oraz innowacyjności w produkcji poprzez integrację systemów cyfrowych, automatyzacji oraz analizy danych. W odróżnieniu od wcześniejszych etapów rozwoju przemysłu, które koncentrowały się głównie na mechanizacji i automatyzacji, przemysł 4.0 stawia na inteligentne fabryki, gdzie maszyny i urządzenia są ze sobą połączone w sieci, co umożliwia wymianę informacji w czasie rzeczywistym. Dzięki temu przedsiębiorstwa mogą lepiej reagować na zmieniające się potrzeby rynku oraz optymalizować swoje procesy produkcyjne. Wprowadzenie przemysłu 4.0 wiąże się z wykorzystaniem technologii takich jak Internet Rzeczy (IoT), sztuczna inteligencja (AI), big data oraz chmura obliczeniowa. Te innowacje pozwalają na zbieranie i analizowanie ogromnych ilości danych, co z kolei prowadzi do podejmowania bardziej świadomych decyzji biznesowych oraz poprawy jakości produktów.
Jakie technologie są kluczowe dla przemysłu 4.0?
W kontekście przemysłu 4.0 kluczowe technologie obejmują szereg innowacyjnych rozwiązań, które zmieniają sposób funkcjonowania zakładów produkcyjnych. Internet Rzeczy (IoT) odgrywa fundamentalną rolę, umożliwiając połączenie maszyn i urządzeń w sieci, co pozwala na monitorowanie ich stanu oraz wydajności w czasie rzeczywistym. Dzięki IoT możliwe jest zbieranie danych z różnych źródeł, co ułatwia analizę i podejmowanie decyzji opartych na faktach. Sztuczna inteligencja (AI) również ma ogromne znaczenie w przemyśle 4.0, ponieważ pozwala na automatyzację procesów oraz przewidywanie awarii maszyn na podstawie analizy danych historycznych. Kolejną istotną technologią jest big data, która umożliwia przetwarzanie ogromnych zbiorów danych generowanych przez maszyny i systemy produkcyjne. Chmura obliczeniowa natomiast oferuje elastyczność i skalowalność potrzebną do przechowywania i analizy tych danych bez konieczności inwestowania w drogi sprzęt lokalny.
Jakie korzyści przynosi wdrożenie przemysłu 4.0?
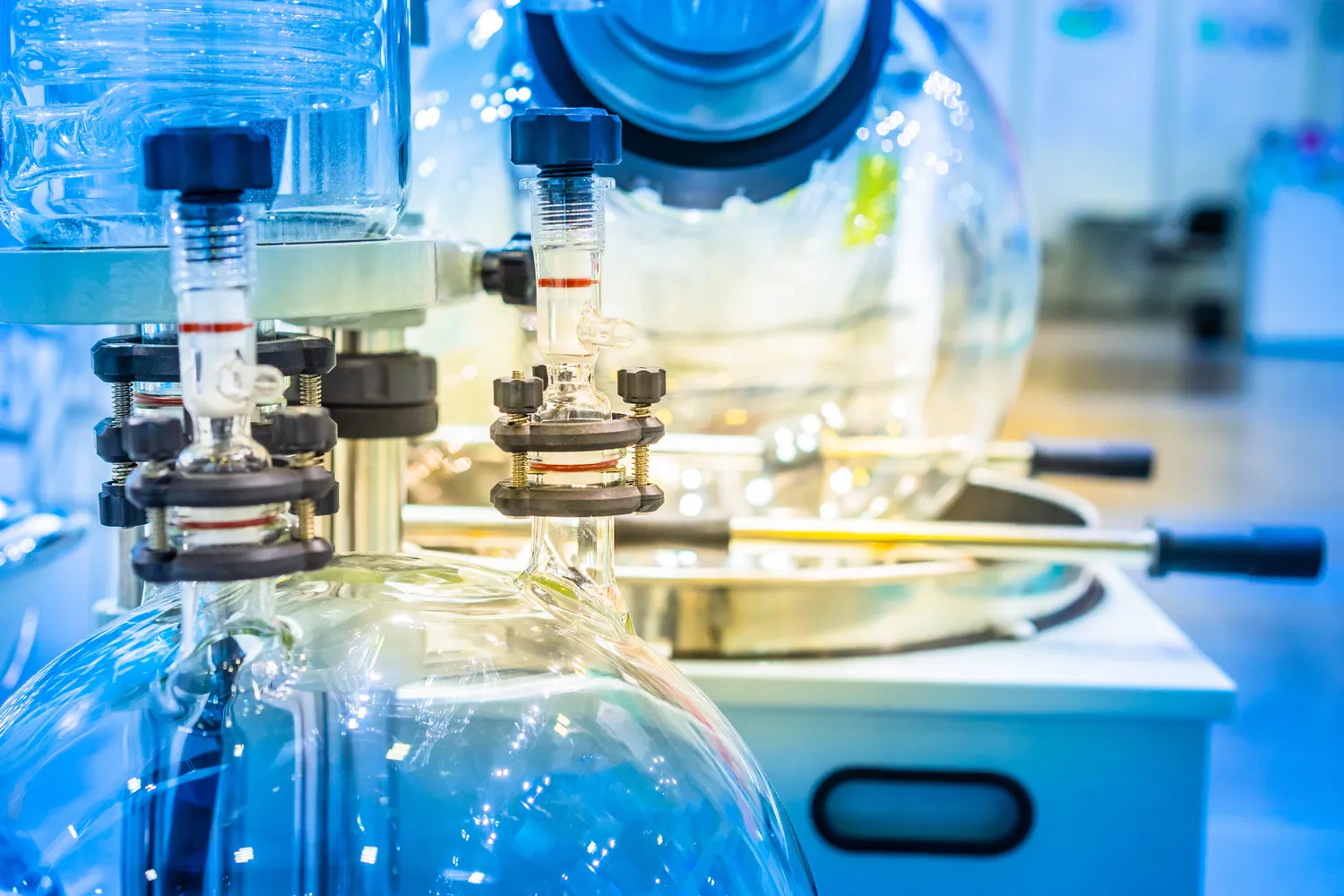
Wdrożenie przemysłu 4.0 niesie ze sobą wiele korzyści dla przedsiębiorstw oraz całej gospodarki. Przede wszystkim zwiększa efektywność procesów produkcyjnych poprzez automatyzację rutynowych zadań oraz optymalizację wykorzystania zasobów. Dzięki zastosowaniu nowoczesnych technologii możliwe jest szybsze wykrywanie problemów oraz ich rozwiązanie, co prowadzi do zmniejszenia przestojów i zwiększenia wydajności linii produkcyjnych. Kolejną zaletą jest poprawa jakości produktów, ponieważ zaawansowane systemy monitorowania pozwalają na bieżąco kontrolować parametry produkcji i eliminować błędy już na etapie wytwarzania. Przemysł 4.0 przyczynia się także do większej elastyczności produkcji, umożliwiając dostosowywanie się do zmieniających się potrzeb klientów oraz szybsze wprowadzanie nowych produktów na rynek. Dodatkowo, dzięki lepszemu zarządzaniu danymi i analizie informacji przedsiębiorstwa mogą podejmować bardziej świadome decyzje strategiczne, co przekłada się na ich konkurencyjność na rynku globalnym.
Jakie wyzwania stoją przed przedsiębiorstwami przy wdrażaniu przemysłu 4.0?
Mimo licznych korzyści związanych z wdrożeniem przemysłu 4.0 istnieje wiele wyzwań, które przedsiębiorstwa muszą pokonać, aby skutecznie zaimplementować te nowoczesne rozwiązania technologiczne. Jednym z głównych problemów jest brak odpowiednich umiejętności wśród pracowników, którzy muszą być przeszkoleni w zakresie obsługi nowych technologii oraz analizy danych. Wiele firm boryka się z niedoborem specjalistów w dziedzinach takich jak programowanie czy analiza danych, co może opóźnić proces transformacji cyfrowej. Kolejnym wyzwaniem jest integracja istniejących systemów z nowymi technologiami; wiele zakładów korzysta z przestarzałych rozwiązań informatycznych, które nie są kompatybilne z nowoczesnymi narzędziami IoT czy AI. Dodatkowo kwestie związane z bezpieczeństwem danych stają się coraz bardziej palące; wraz z rosnącą ilością połączonych urządzeń wzrasta ryzyko cyberataków oraz kradzieży danych osobowych czy firmowych informacji strategicznych.
Jakie są przykłady zastosowania przemysłu 4.0 w praktyce?
Przemysł 4.0 znajduje zastosowanie w różnych branżach, co pozwala na zwiększenie efektywności i innowacyjności procesów produkcyjnych. W sektorze motoryzacyjnym wiele firm wdraża inteligentne fabryki, gdzie roboty współpracujące montują pojazdy obok ludzi, co zwiększa wydajność produkcji oraz poprawia bezpieczeństwo pracy. Przykładem może być firma BMW, która wykorzystuje technologie IoT do monitorowania stanu maszyn oraz analizy danych w czasie rzeczywistym, co pozwala na szybsze wykrywanie usterek i optymalizację procesów. W przemyśle spożywczym firmy takie jak Nestlé stosują zaawansowane systemy zarządzania danymi, które umożliwiają śledzenie jakości surowców oraz monitorowanie procesów produkcyjnych, co przekłada się na lepszą jakość produktów końcowych. W branży odzieżowej marki takie jak Zara korzystają z technologii big data do analizy trendów rynkowych oraz preferencji klientów, co pozwala na szybsze dostosowywanie oferty do zmieniających się potrzeb rynku. Wreszcie w sektorze energetycznym firmy takie jak Siemens wdrażają inteligentne sieci energetyczne, które umożliwiają efektywne zarządzanie produkcją i dystrybucją energii, a także integrację odnawialnych źródeł energii.
Jakie umiejętności są potrzebne w erze przemysłu 4.0?
W erze przemysłu 4.0 kluczowe staje się posiadanie odpowiednich umiejętności, które pozwolą pracownikom dostosować się do zmieniającego się środowiska pracy. Przede wszystkim niezbędna jest wiedza z zakresu technologii informacyjnej oraz programowania, ponieważ wiele procesów produkcyjnych opiera się na zaawansowanych systemach komputerowych i automatyzacji. Umiejętności analizy danych również stają się coraz bardziej cenione; pracownicy muszą być w stanie interpretować dane generowane przez maszyny oraz podejmować decyzje na ich podstawie. Dodatkowo ważne jest zrozumienie zasad funkcjonowania Internetu Rzeczy (IoT) oraz sztucznej inteligencji (AI), co pozwoli na efektywne wykorzystanie tych technologii w codziennej pracy. W kontekście pracy zespołowej umiejętności komunikacyjne oraz zdolność do współpracy z różnymi działami w firmie stają się kluczowe, ponieważ transformacja cyfrowa wymaga współdziałania specjalistów z różnych dziedzin.
Jakie są przyszłe kierunki rozwoju przemysłu 4.0?
Przemysł 4.0 rozwija się w szybkim tempie, a przyszłość tej rewolucji przemysłowej zapowiada się obiecująco dzięki dalszym innowacjom technologicznym oraz rosnącemu zainteresowaniu przedsiębiorstw transformacją cyfrową. Jednym z kluczowych kierunków rozwoju jest dalsza automatyzacja procesów produkcyjnych poprzez zastosowanie robotów autonomicznych oraz sztucznej inteligencji, co pozwoli na jeszcze większą efektywność i redukcję kosztów operacyjnych. Kolejnym istotnym trendem będzie rozwój Internetu Rzeczy (IoT), który umożliwi jeszcze głębszą integrację urządzeń i maszyn w sieci oraz zbieranie danych z różnych źródeł w czasie rzeczywistym. Technologie takie jak blockchain mogą również odegrać ważną rolę w zapewnieniu bezpieczeństwa danych oraz transparentności procesów produkcyjnych. W miarę jak przedsiębiorstwa będą coraz bardziej polegały na analizie danych, rozwój narzędzi do przetwarzania big data stanie się kluczowy dla podejmowania decyzji strategicznych. Zrównoważony rozwój i odpowiedzialność społeczna również będą miały znaczenie; firmy będą musiały dostosować swoje strategie do oczekiwań konsumentów dotyczących ekologii i etyki biznesowej.
Jakie są różnice między przemysłem 4.0 a wcześniejszymi rewolucjami przemysłowymi?
Przemysł 4.0 różni się od wcześniejszych rewolucji przemysłowych pod wieloma względami, zarówno technologicznymi, jak i organizacyjnymi. Pierwsza rewolucja przemysłowa koncentrowała się głównie na mechanizacji procesów produkcyjnych przy użyciu pary wodnej i maszyn mechanicznych, co znacznie zwiększyło wydajność pracy ludzkiej. Druga rewolucja przyniosła elektryczność i liniową produkcję masową, co umożliwiło dalszą automatyzację i standaryzację produktów. Trzecia rewolucja to era cyfryzacji, która wprowadziła komputery oraz automatyzację procesów przy użyciu technologii elektronicznych, jednak nadal opierała się na tradycyjnych modelach produkcji. Przemysł 4.0 natomiast kładzie nacisk na pełną integrację systemów cyfrowych z fizycznymi procesami produkcyjnymi poprzez zastosowanie Internetu Rzeczy (IoT), sztucznej inteligencji (AI) oraz analizy big data. To podejście umożliwia tworzenie inteligentnych fabryk, gdzie maszyny komunikują się ze sobą i podejmują decyzje autonomicznie, co prowadzi do znacznie większej elastyczności i szybkości reakcji na zmieniające się potrzeby rynku.
Jakie są perspektywy zatrudnienia w kontekście przemysłu 4.0?
Perspektywy zatrudnienia w kontekście przemysłu 4.0 są złożone i obejmują zarówno wyzwania, jak i nowe możliwości dla pracowników różnych branż. Z jednej strony automatyzacja procesów może prowadzić do redukcji miejsc pracy w niektórych sektorach, zwłaszcza tych opartych na rutynowych zadaniach manualnych lub prostych operacjach produkcyjnych. Z drugiej strony jednak rozwój nowych technologii stwarza zapotrzebowanie na specjalistów z zakresu IT, analizy danych oraz inżynierii robotyki, co może prowadzić do powstania nowych miejsc pracy wymagających zaawansowanych umiejętności technicznych. Firmy będą potrzebowały pracowników zdolnych do obsługi nowoczesnych systemów oraz interpretacji danych generowanych przez maszyny, co oznacza konieczność inwestycji w edukację i szkolenia dla obecnych pracowników oraz młodych adeptów rynku pracy.
Jakie są najważniejsze trendy związane z rozwojem przemysłu 4.0?
Rozwój przemysłu 4.0 wiąże się z wieloma istotnymi trendami technologicznymi oraz organizacyjnymi, które mają wpływ na sposób funkcjonowania przedsiębiorstw na całym świecie. Jednym z najważniejszych trendów jest rosnąca popularność sztucznej inteligencji (AI) oraz uczenia maszynowego; technologie te pozwalają na automatyzację procesów decyzyjnych oraz przewidywanie awarii maszyn na podstawie analizy danych historycznych. Kolejnym istotnym trendem jest rozwój Internetu Rzeczy (IoT), który umożliwia połączenie urządzeń i maszyn w sieci oraz zbieranie danych o ich wydajności w czasie rzeczywistym; to z kolei prowadzi do lepszego zarządzania zasobami oraz optymalizacji procesów produkcyjnych.