Destylator przemysłowy to urządzenie wykorzystywane do separacji cieczy na podstawie różnicy w temperaturze wrzenia. Proces ten polega na podgrzewaniu cieczy, co powoduje jej parowanie, a następnie skraplaniu powstałych par, co pozwala na uzyskanie czystych frakcji. W przemyśle destylatory są wykorzystywane do produkcji różnych substancji chemicznych, w tym alkoholi, olejów eterycznych oraz rozpuszczalników. W zależności od zastosowania, destylatory mogą mieć różne konstrukcje i rozmiary. Na przykład, w przemyśle spożywczym często stosuje się destylatory kolumnowe, które umożliwiają uzyskanie wysokiej czystości produktów. W procesie destylacji kluczową rolę odgrywa temperatura, ponieważ różne substancje mają różne temperatury wrzenia. Dobrze zaprojektowany destylator pozwala na efektywne oddzielanie składników nawet w przypadku złożonych mieszanin.
Jakie są rodzaje destylatorów przemysłowych i ich zastosowania
W przemyśle istnieje wiele rodzajów destylatorów, które różnią się konstrukcją oraz przeznaczeniem. Najpopularniejsze z nich to destylatory prostokątne, kolumnowe oraz próżniowe. Destylatory prostokątne są najprostsze w budowie i najczęściej stosowane w małych zakładach produkcyjnych. Umożliwiają one podstawową separację cieczy i są łatwe w obsłudze. Z kolei destylatory kolumnowe charakteryzują się bardziej skomplikowaną budową i są używane w dużych zakładach przemysłowych do produkcji wysokiej jakości substancji chemicznych. Dzięki zastosowaniu kolumny z różnymi poziomami kondensacji możliwe jest uzyskanie wielu frakcji o różnych właściwościach. Destylatory próżniowe natomiast działają w obniżonym ciśnieniu, co pozwala na destylację substancji o wysokiej temperaturze wrzenia bez ryzyka ich degradacji.
Jakie są zalety korzystania z destylatorów przemysłowych
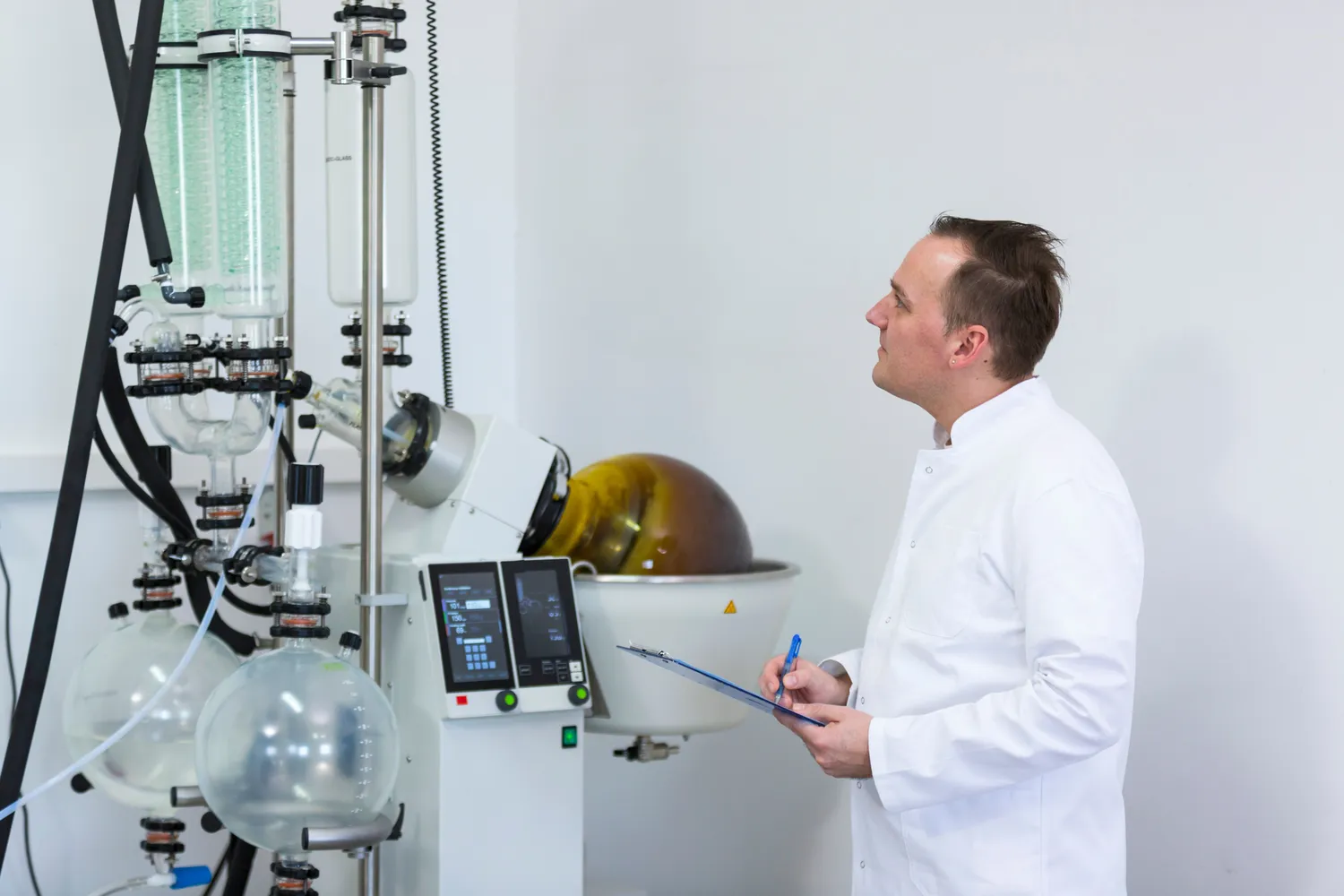
Korzystanie z destylatorów przemysłowych niesie ze sobą wiele korzyści dla producentów oraz całego procesu produkcyjnego. Przede wszystkim umożliwiają one uzyskanie wysokiej czystości produktów, co jest kluczowe w wielu branżach, takich jak farmaceutyka czy chemia. Dzięki precyzyjnemu oddzieleniu składników możliwe jest zwiększenie efektywności procesów produkcyjnych oraz redukcja strat materiałowych. Kolejną zaletą jest możliwość skalowania procesu – nowoczesne destylatory mogą być dostosowane do różnych wielkości produkcji, co sprawia, że są elastyczne i mogą rosnąć wraz z potrzebami firmy. Ponadto, wiele współczesnych urządzeń wyposażonych jest w zaawansowane systemy automatyzacji, co pozwala na monitorowanie i kontrolowanie procesu w czasie rzeczywistym. Dzięki temu można szybko reagować na zmiany warunków pracy oraz optymalizować parametry procesu, co przekłada się na oszczędności energetyczne i surowcowe.
Jakie wyzwania wiążą się z użytkowaniem destylatorów przemysłowych
Mimo licznych zalet użytkowanie destylatorów przemysłowych wiąże się także z pewnymi wyzwaniami. Jednym z głównych problemów jest konieczność regularnej konserwacji i czyszczenia urządzeń, aby zapewnić ich prawidłowe działanie oraz uniknąć kontaminacji produktów końcowych. Z czasem osady mogą gromadzić się wewnątrz kolumny lub wymienników ciepła, co prowadzi do obniżenia efektywności procesu destylacji. Dodatkowo, operatorzy muszą być odpowiednio przeszkoleni w zakresie obsługi tych skomplikowanych urządzeń, co może generować dodatkowe koszty dla przedsiębiorstwa. Innym wyzwaniem jest zarządzanie zużyciem energii – proces destylacji może być energochłonny, a nieefektywne systemy mogą prowadzić do znacznych wydatków operacyjnych. Ważnym aspektem jest również przestrzeganie norm bezpieczeństwa związanych z pracą z substancjami chemicznymi oraz wysokimi temperaturami.
Jakie są najnowsze technologie w destylacji przemysłowej
W ostatnich latach branża destylacji przemysłowej zyskała na znaczeniu dzięki wprowadzeniu nowoczesnych technologii, które znacznie poprawiają efektywność i jakość procesów. Jednym z najważniejszych trendów jest automatyzacja procesów destylacyjnych, która pozwala na zdalne monitorowanie i kontrolowanie parametrów pracy urządzeń. Dzięki zastosowaniu czujników oraz systemów informatycznych, operatorzy mogą w czasie rzeczywistym śledzić zmiany w temperaturze, ciśnieniu czy składzie chemicznym mieszanin. To z kolei umożliwia szybką reakcję na ewentualne problemy oraz optymalizację procesu, co przekłada się na oszczędności surowcowe i energetyczne. Kolejną innowacją są destylatory oparte na technologii membranowej, które oferują alternatywę dla tradycyjnych metod separacji. Te nowoczesne urządzenia działają na zasadzie selektywnego przepuszczania cząsteczek przez membrany, co pozwala na uzyskanie wysokiej czystości produktów przy niższym zużyciu energii. Inwestycje w badania i rozwój w dziedzinie destylacji prowadzą również do powstawania nowych materiałów konstrukcyjnych, które zwiększają trwałość i efektywność urządzeń.
Jakie są koszty inwestycji w destylatory przemysłowe
Inwestycja w destylatory przemysłowe wiąże się z różnorodnymi kosztami, które należy uwzględnić przed podjęciem decyzji o zakupie. Koszt samego urządzenia może być znaczny i zależy od jego typu, wielkości oraz zaawansowania technologicznego. Na przykład, prostsze modele mogą kosztować kilkadziesiąt tysięcy złotych, podczas gdy bardziej skomplikowane destylatory kolumnowe mogą osiągać ceny rzędu setek tysięcy złotych. Oprócz kosztu zakupu należy również uwzględnić wydatki związane z instalacją oraz uruchomieniem urządzenia, które mogą obejmować prace budowlane oraz dostosowanie infrastruktury zakładu do wymagań nowego sprzętu. Dodatkowo, przedsiębiorstwa muszą zainwestować w szkolenie personelu odpowiedzialnego za obsługę destylatorów, co również generuje dodatkowe koszty. Należy także pamiętać o bieżących wydatkach operacyjnych związanych z eksploatacją urządzeń, takich jak zużycie energii, konserwacja czy zakup surowców do procesu destylacji.
Jakie są kluczowe czynniki wpływające na wybór destylatora przemysłowego
Wybór odpowiedniego destylatora przemysłowego to kluczowy krok dla każdej firmy zajmującej się produkcją chemiczną lub spożywczą. Istnieje wiele czynników, które należy wziąć pod uwagę przy podejmowaniu tej decyzji. Przede wszystkim istotne jest określenie rodzaju substancji, które będą poddawane procesowi destylacji. Różne substancje mają różne właściwości fizykochemiczne, co wpływa na wybór odpowiedniego typu destylatora. Kolejnym ważnym czynnikiem jest pożądana czystość końcowego produktu – jeśli firma potrzebuje substancji o wysokiej czystości, konieczne będzie zainwestowanie w bardziej zaawansowane technologie. Warto również rozważyć skalowalność urządzenia – jeśli planujesz rozwój produkcji w przyszłości, dobrze jest wybrać model, który można łatwo dostosować do rosnących potrzeb. Koszt zakupu oraz eksploatacji to kolejny kluczowy aspekt – przedsiębiorstwa powinny dokładnie przeanalizować swoje możliwości finansowe oraz przewidywane wydatki operacyjne związane z użytkowaniem destylatora.
Jakie są zastosowania destylatorów przemysłowych w różnych branżach
Destylatory przemysłowe znajdują szerokie zastosowanie w wielu branżach gospodarki, co sprawia, że ich rola jest niezwykle istotna dla funkcjonowania współczesnej produkcji. W przemyśle chemicznym wykorzystuje się je do produkcji różnorodnych substancji chemicznych, takich jak rozpuszczalniki czy alkohole etylowe. Destylacja jest kluczowym procesem w produkcji wysokiej jakości alkoholi spożywczych oraz napojów alkoholowych, gdzie precyzyjne oddzielanie frakcji ma ogromne znaczenie dla smaku i aromatu finalnych produktów. W przemyśle farmaceutycznym natomiast stosuje się destylatory do oczyszczania substancji czynnych oraz produkcji leków o wysokiej czystości. W branży petrochemicznej proces destylacji służy do separacji różnych frakcji ropy naftowej, co pozwala na uzyskanie paliw oraz innych produktów petrochemicznych. Ponadto destylatory znajdują zastosowanie w przemyśle kosmetycznym do ekstrakcji olejków eterycznych oraz innych składników aktywnych wykorzystywanych w produkcji kosmetyków.
Jakie są przyszłe kierunki rozwoju technologii destylacji przemysłowej
Przyszłość technologii destylacji przemysłowej zapowiada się obiecująco dzięki ciągłemu rozwojowi innowacyjnych rozwiązań i metod produkcji. W miarę jak rośnie świadomość ekologiczna społeczeństwa oraz potrzeba zmniejszenia wpływu przemysłu na środowisko naturalne, coraz więcej firm stawia na zrównoważony rozwój i wdrażanie technologii przyjaznych dla środowiska. W kontekście destylacji oznacza to poszukiwanie bardziej efektywnych energetycznie procesów oraz materiałów konstrukcyjnych o mniejszym śladzie węglowym. Również rozwój technologii cyfrowych otwiera nowe możliwości dla automatyzacji procesów oraz analizy danych operacyjnych, co pozwala na jeszcze lepsze zarządzanie produkcją i optymalizację kosztów. Możliwości zastosowania sztucznej inteligencji do prognozowania wydajności czy identyfikowania potencjalnych problemów mogą znacząco wpłynąć na przyszłość branży.
Jakie są najczęstsze błędy przy użytkowaniu destylatorów przemysłowych
Użytkowanie destylatorów przemysłowych wiąże się z wieloma wyzwaniami i pułapkami, które mogą prowadzić do nieefektywności procesu lub nawet awarii urządzenia. Jednym z najczęstszych błędów jest niewłaściwe ustawienie parametrów pracy urządzenia, takich jak temperatura czy ciśnienie. Niezgodność tych parametrów z wymaganiami procesu może prowadzić do obniżenia jakości końcowego produktu lub nawet uszkodzenia sprzętu. Kolejnym powszechnym problemem jest brak regularnej konserwacji i czyszczenia urządzeń – osady gromadzące się wewnątrz kolumny mogą znacząco obniżyć efektywność procesu i prowadzić do awarii. Często zdarza się także niedostateczne przeszkolenie personelu obsługującego urządzenia; brak wiedzy na temat działania destylatorów może prowadzić do błędnych decyzji operacyjnych i zwiększać ryzyko wystąpienia incydentów związanych z bezpieczeństwem pracy.