Budowa maszyn produkcyjnych to złożony proces, który obejmuje wiele kluczowych elementów. W pierwszej kolejności należy zwrócić uwagę na konstrukcję mechaniczną, która stanowi podstawę każdej maszyny. To właśnie ona odpowiada za stabilność i wytrzymałość urządzenia, co jest szczególnie istotne w kontekście intensywnej eksploatacji w środowisku przemysłowym. Kolejnym ważnym aspektem jest system napędowy, który zapewnia odpowiednią moc i prędkość działania maszyny. W zależności od przeznaczenia maszyny, może to być napęd elektryczny, hydrauliczny lub pneumatyczny. Również układy sterowania odgrywają kluczową rolę w budowie maszyn produkcyjnych, umożliwiając precyzyjne zarządzanie ich pracą oraz integrację z innymi systemami. Nie można zapomnieć o elementach bezpieczeństwa, które są niezbędne do ochrony operatorów oraz samego urządzenia przed awariami czy uszkodzeniami.
Jakie są najczęstsze zastosowania maszyn produkcyjnych
Maszyny produkcyjne znajdują zastosowanie w wielu branżach przemysłowych, co czyni je niezwykle wszechstronnymi narzędziami. W przemyśle motoryzacyjnym wykorzystuje się je do montażu poszczególnych komponentów samochodowych, co pozwala na zwiększenie wydajności produkcji oraz redukcję błędów ludzkich. W sektorze spożywczym maszyny te służą do pakowania, etykietowania oraz przetwarzania żywności, co ma kluczowe znaczenie dla zachowania jakości produktów oraz ich bezpieczeństwa. W branży elektronicznej maszyny produkcyjne są wykorzystywane do montażu skomplikowanych układów elektronicznych, co wymaga precyzyjnego działania i zaawansowanej technologii. Również w przemyśle chemicznym maszyny te odgrywają istotną rolę w procesach mieszania, reakcji chemicznych oraz pakowania substancji chemicznych.
Jakie technologie są stosowane w budowie maszyn produkcyjnych
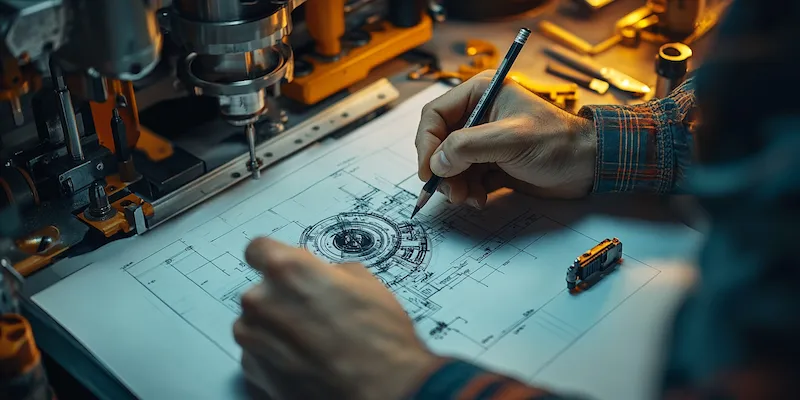
W budowie maszyn produkcyjnych wykorzystywane są różnorodne technologie, które mają na celu zwiększenie efektywności oraz precyzji działania tych urządzeń. Jedną z najważniejszych technologii jest automatyka przemysłowa, która pozwala na zautomatyzowanie wielu procesów produkcyjnych. Dzięki zastosowaniu czujników, aktuatorów oraz systemów sterowania możliwe jest monitorowanie i kontrolowanie pracy maszyn w czasie rzeczywistym. Kolejną istotną technologią jest robotyka, która umożliwia wykorzystanie robotów przemysłowych do wykonywania skomplikowanych zadań montażowych czy pakujących. Roboty te charakteryzują się dużą precyzją oraz zdolnością do pracy w trudnych warunkach. W ostatnich latach coraz większą popularność zdobywa także technologia druku 3D, która pozwala na szybkie prototypowanie oraz produkcję części zamiennych bez potrzeby tworzenia kosztownych form. Dodatkowo rozwój sztucznej inteligencji i uczenia maszynowego otwiera nowe możliwości w zakresie optymalizacji procesów produkcyjnych oraz przewidywania awarii maszyn.
Jakie są wyzwania związane z budową maszyn produkcyjnych
Budowa maszyn produkcyjnych wiąże się z wieloma wyzwaniami, które mogą wpłynąć na efektywność ich działania oraz koszty produkcji. Jednym z głównych problemów jest konieczność dostosowania maszyn do szybko zmieniających się potrzeb rynku oraz technologii. Firmy muszą inwestować w badania i rozwój, aby nadążyć za nowinkami technologicznymi oraz wymaganiami klientów. Kolejnym wyzwaniem jest zapewnienie wysokiej jakości materiałów używanych do budowy maszyn, co ma kluczowe znaczenie dla ich trwałości i niezawodności. Problemy związane z jakością mogą prowadzić do awarii oraz zwiększenia kosztów serwisowania urządzeń. Również integracja nowych technologii z istniejącymi systemami może być skomplikowana i czasochłonna, co wymaga odpowiedniego planowania i zasobów ludzkich. Dodatkowo firmy muszą zmierzyć się z rosnącymi wymaganiami dotyczącymi ochrony środowiska oraz bezpieczeństwa pracy, co często wiąże się z dodatkowymi kosztami i zmianami w procesach produkcyjnych.
Jakie są kluczowe etapy projektowania maszyn produkcyjnych
Projektowanie maszyn produkcyjnych to proces, który składa się z kilku kluczowych etapów, każdy z nich mający istotne znaczenie dla końcowego efektu. Pierwszym krokiem jest analiza potrzeb klienta oraz specyfikacji technicznych, które pozwalają na określenie wymagań dotyczących funkcjonalności maszyny. Na tym etapie inżynierowie zbierają informacje o procesach produkcyjnych, w których maszyna ma być wykorzystywana, co pozwala na lepsze dopasowanie projektu do rzeczywistych potrzeb. Kolejnym etapem jest koncepcja i wstępne projektowanie, które obejmuje tworzenie szkiców oraz modeli 3D. W tym momencie ważne jest uwzględnienie wszystkich aspektów konstrukcyjnych, takich jak materiały, mechanizmy napędowe oraz systemy sterowania. Po zatwierdzeniu koncepcji następuje faza szczegółowego projektowania, gdzie opracowywane są wszystkie niezbędne dokumentacje techniczne oraz rysunki wykonawcze. Następnie przechodzi się do etapu prototypowania, gdzie tworzony jest pierwszy model maszyny. Prototyp jest testowany pod kątem wydajności oraz niezawodności, co pozwala na wprowadzenie ewentualnych poprawek przed rozpoczęciem produkcji seryjnej.
Jakie są najnowsze trendy w budowie maszyn produkcyjnych
W ostatnich latach w budowie maszyn produkcyjnych można zaobserwować wiele interesujących trendów, które mają na celu zwiększenie efektywności oraz innowacyjności w przemyśle. Jednym z najważniejszych trendów jest automatyzacja procesów produkcyjnych, która pozwala na zredukowanie kosztów pracy oraz zwiększenie wydajności. Wprowadzenie robotów przemysłowych do linii produkcyjnych stało się standardem w wielu branżach, co umożliwia szybsze i bardziej precyzyjne wykonywanie zadań. Również rozwój technologii Internetu Rzeczy (IoT) wpływa na sposób działania maszyn produkcyjnych. Dzięki możliwości podłączenia urządzeń do sieci możliwe jest monitorowanie ich pracy w czasie rzeczywistym oraz zbieranie danych analitycznych, co pozwala na optymalizację procesów i przewidywanie awarii. Kolejnym istotnym trendem jest zrównoważony rozwój i ekologia, co prowadzi do poszukiwania rozwiązań minimalizujących wpływ produkcji na środowisko. Firmy coraz częściej inwestują w technologie energooszczędne oraz materiały przyjazne dla środowiska. Wreszcie, personalizacja maszyn staje się coraz bardziej popularna, co pozwala na dostosowanie urządzeń do indywidualnych potrzeb klientów i specyfiki ich działalności.
Jakie są kluczowe czynniki wpływające na wybór maszyn produkcyjnych
Wybór odpowiednich maszyn produkcyjnych to decyzja, która ma ogromny wpływ na efektywność całego procesu produkcji. Istnieje wiele czynników, które należy wziąć pod uwagę przy podejmowaniu tej decyzji. Przede wszystkim należy zwrócić uwagę na specyfikę produkcji oraz wymagania dotyczące wydajności i jakości produktów. Maszyny muszą być dostosowane do rodzaju materiałów oraz technologii wykorzystywanych w danym procesie. Kolejnym istotnym czynnikiem jest koszt zakupu oraz eksploatacji maszyny. Firmy muszą dokładnie analizować swoje możliwości finansowe oraz przewidywać koszty związane z serwisowaniem i utrzymaniem urządzenia w dobrym stanie technicznym. Również dostępność części zamiennych oraz wsparcia technicznego ma kluczowe znaczenie dla zapewnienia ciągłości produkcji. Dodatkowo warto zwrócić uwagę na elastyczność maszyny, która pozwoli na dostosowanie jej do zmieniających się potrzeb rynku i technologii.
Jakie są korzyści płynące z modernizacji maszyn produkcyjnych
Modernizacja maszyn produkcyjnych to proces, który przynosi wiele korzyści zarówno dla przedsiębiorstw, jak i dla samych pracowników. Jedną z głównych zalet modernizacji jest zwiększenie wydajności urządzeń, co przekłada się na wyższą produktywność linii produkcyjnej. Dzięki zastosowaniu nowoczesnych technologii możliwe jest osiągnięcie lepszej jakości produktów oraz redukcja czasu cyklu produkcyjnego. Modernizacja często wiąże się także z obniżeniem kosztów eksploatacji maszyn poprzez zastosowanie energooszczędnych rozwiązań oraz materiałów o lepszych parametrach technicznych. Kolejną korzyścią jest poprawa bezpieczeństwa pracy operatorów dzięki wdrożeniu nowoczesnych systemów zabezpieczeń oraz ergonomicznych rozwiązań konstrukcyjnych. Pracownicy mogą czuć się bardziej komfortowo i bezpiecznie podczas obsługi nowoczesnych urządzeń, co wpływa na ich satysfakcję z pracy oraz obniża ryzyko wypadków. Dodatkowo modernizacja maszyn może przyczynić się do zwiększenia konkurencyjności firmy na rynku poprzez możliwość szybszego reagowania na zmieniające się potrzeby klientów oraz dostosowywania oferty produktowej do aktualnych trendów rynkowych.
Jakie są różnice między maszynami standardowymi a specjalistycznymi
Maszyny produkcyjne można podzielić na dwie główne kategorie: standardowe i specjalistyczne, które różnią się od siebie pod wieloma względami. Maszyny standardowe to urządzenia zaprojektowane z myślą o szerokim zakresie zastosowań i uniwersalności. Często stosowane są w różnych branżach przemysłowych i mogą być łatwo dostosowywane do różnych procesów produkcyjnych poprzez wymianę narzędzi czy akcesoriów. Dzięki swojej wszechstronności znajdują zastosowanie w wielu zakładach produkcyjnych, co czyni je popularnym wyborem dla firm rozpoczynających działalność lub poszukujących elastycznych rozwiązań. Z kolei maszyny specjalistyczne są projektowane z myślą o konkretnych zadaniach lub branżach i charakteryzują się zaawansowanymi funkcjami dostosowanymi do specyficznych potrzeb użytkowników. Często oferują one wyższą wydajność oraz jakość produktów niż maszyny standardowe, jednak ich koszt zakupu może być znacznie wyższy.
Jakie umiejętności są niezbędne przy obsłudze maszyn produkcyjnych
Obsługa maszyn produkcyjnych wymaga od pracowników szeregu umiejętności technicznych oraz interpersonalnych, które są niezbędne do zapewnienia efektywnej i bezpiecznej pracy w zakładzie przemysłowym. Przede wszystkim operatorzy muszą posiadać wiedzę techniczną dotyczącą działania maszyn oraz ich budowy, aby móc skutecznie diagnozować ewentualne problemy czy awarie podczas pracy. Umiejętność czytania rysunków technicznych i schematów elektrycznych również jest kluczowa dla prawidłowego wykonywania obowiązków związanych z obsługą urządzeń. Ponadto operatorzy powinni być zaznajomieni z zasadami bezpieczeństwa pracy i procedurami awaryjnymi, aby minimalizować ryzyko wypadków i zapewnić sobie oraz innym pracownikom bezpieczeństwo podczas eksploatacji maszyn. Dobrze rozwinięte umiejętności komunikacyjne są również istotne, ponieważ operatorzy często współpracują z innymi członkami zespołu oraz działami technicznymi w celu rozwiązywania problemów czy optymalizacji procesów produkcyjnych.