Łączenie dwóch kompresorów to proces, który może znacząco zwiększyć wydajność systemu pneumatycznego. W pierwszej kolejności, przed przystąpieniem do pracy, należy dokładnie zaplanować, jak będą one ze sobą współpracować. Kluczowym krokiem jest określenie, czy kompresory będą działały równolegle, czy szeregowo. W przypadku połączenia równoległego obydwa urządzenia pracują jednocześnie, co pozwala na zwiększenie wydajności powietrza dostarczanego do systemu. Z kolei połączenie szeregowe polega na tym, że jeden kompresor zasila drugi, co może być korzystne w sytuacjach wymagających wyższego ciśnienia. Ważne jest również, aby upewnić się, że oba kompresory mają podobne parametry techniczne, takie jak ciśnienie robocze oraz wydajność. Należy także zwrócić uwagę na odpowiednie złącza i rury, które będą używane do połączenia urządzeń.
Jakie narzędzia są potrzebne do łączenia kompresorów?
Aby skutecznie połączyć dwa kompresory, konieczne jest posiadanie odpowiednich narzędzi oraz akcesoriów. Przede wszystkim warto zaopatrzyć się w klucze płaskie i nasadowe, które umożliwią dokręcenie wszystkich połączeń. Dodatkowo przydatna będzie wkrętarka elektryczna lub ręczna, która ułatwi montaż elementów mocujących. Niezbędne będą także złączki pneumatyczne oraz rury o odpowiedniej średnicy, które będą mogły pomieścić przepływ powietrza z obu kompresorów. Warto również mieć pod ręką uszczelki oraz taśmy teflonowe, które pomogą w uszczelnieniu połączeń i zapobiegną wyciekom powietrza. Nie można zapomnieć o narzędziach do cięcia rur oraz ich wyginania, jeśli zajdzie taka potrzeba. Bezpieczeństwo podczas pracy jest kluczowe, dlatego zawsze należy mieć na sobie odpowiednią odzież ochronną oraz okulary zabezpieczające.
Jakie są najważniejsze zasady bezpieczeństwa przy łączeniu kompresorów?
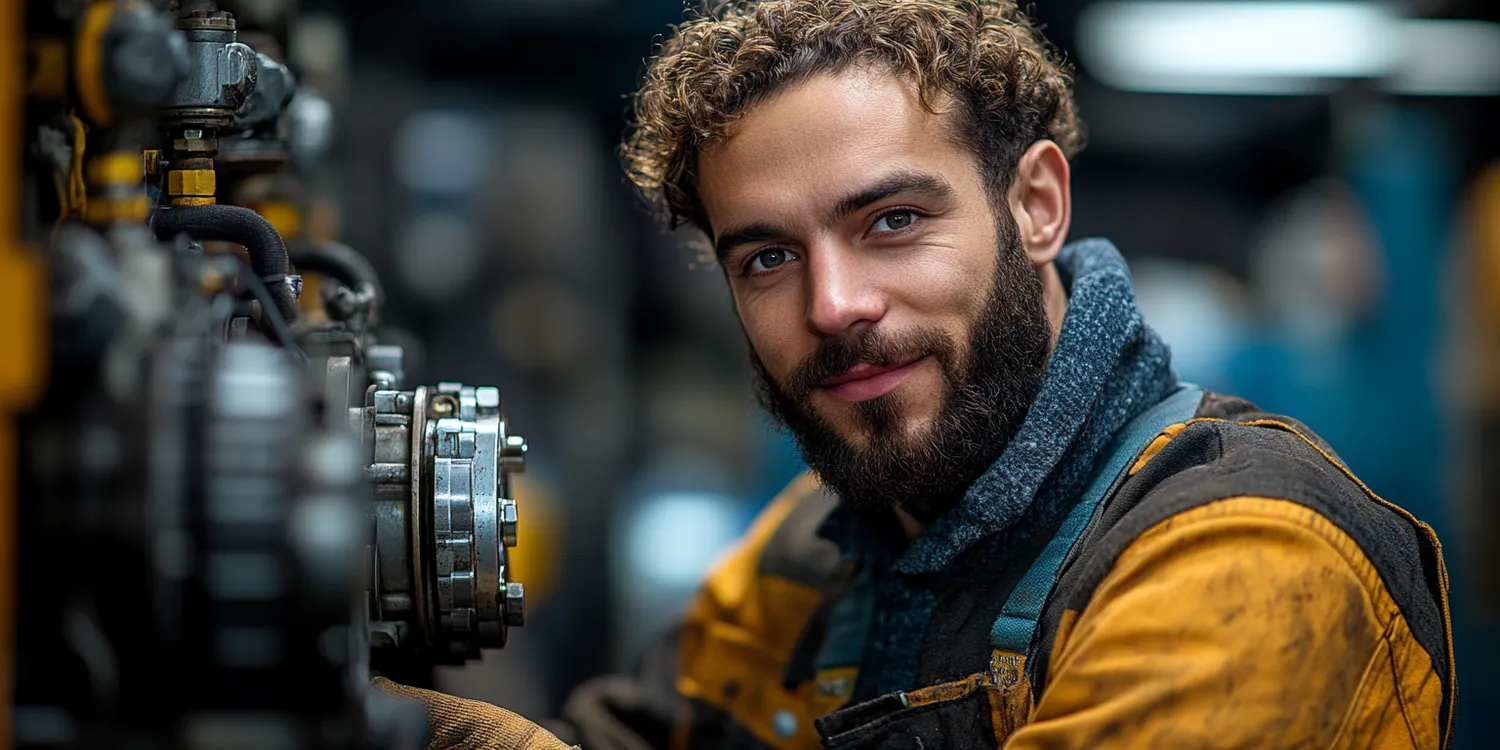
Bezpieczeństwo podczas łączenia dwóch kompresorów jest niezwykle istotne i nie można go bagatelizować. Przede wszystkim przed przystąpieniem do pracy należy upewnić się, że oba urządzenia są wyłączone i odłączone od źródła zasilania. To podstawowa zasada, która pozwoli uniknąć niebezpiecznych sytuacji związanych z przypadkowym uruchomieniem sprzętu. Kolejnym krokiem jest sprawdzenie stanu technicznego kompresorów oraz ich przewodów – wszelkie uszkodzenia mogą prowadzić do poważnych awarii lub wypadków. Ważne jest także stosowanie się do instrukcji producenta dotyczących łączenia urządzeń oraz ich eksploatacji. Podczas pracy warto mieć kogoś w pobliżu, kto będzie mógł udzielić pomocy w razie potrzeby. Używanie odpowiednich narzędzi ochronnych takich jak rękawice czy gogle to kolejny element dbania o bezpieczeństwo.
Jakie są korzyści z łączenia dwóch kompresorów?
Łączenie dwóch kompresorów niesie ze sobą wiele korzyści, które mogą znacząco poprawić efektywność pracy w różnych branżach. Po pierwsze, zwiększona wydajność powietrza to jedna z najważniejszych zalet tego rozwiązania. Dzięki połączeniu dwóch jednostek można uzyskać większy przepływ powietrza oraz wyższe ciśnienie robocze, co przekłada się na lepszą obsługę narzędzi pneumatycznych oraz innych urządzeń wymagających sprężonego powietrza. Dodatkowo łączenie kompresorów może prowadzić do oszczędności energii – w przypadku awarii jednego z urządzeń drugie może przejąć jego funkcje, co minimalizuje przestoje i straty finansowe związane z brakiem dostępu do sprężonego powietrza. Co więcej, możliwość rozbudowy systemu o dodatkowe kompresory w przyszłości daje elastyczność i możliwość dostosowania się do rosnących potrzeb produkcyjnych lub usługowych firmy.
Jakie są najczęstsze błędy przy łączeniu kompresorów?
Podczas łączenia dwóch kompresorów istnieje wiele pułapek, w które można łatwo wpaść, co może prowadzić do nieefektywności lub nawet uszkodzenia sprzętu. Jednym z najczęstszych błędów jest niewłaściwe dobranie parametrów technicznych obu kompresorów. Użycie urządzeń o różnych ciśnieniach roboczych lub wydajnościach może prowadzić do nierównomiernego obciążenia, co w dłuższej perspektywie może skutkować awarią jednego z nich. Kolejnym problemem jest niewłaściwe połączenie przewodów i złączek. Nieszczelności w systemie mogą prowadzić do utraty ciśnienia oraz marnotrawstwa energii, co negatywnie wpłynie na efektywność całego układu. Często zdarza się również, że użytkownicy nie przestrzegają zasad bezpieczeństwa, co może prowadzić do poważnych wypadków. Ignorowanie instrukcji producenta to kolejny błąd, który może skutkować nieprawidłowym działaniem kompresorów.
Jakie są różnice między kompresorami tłokowymi a śrubowymi?
Wybór odpowiedniego typu kompresora jest kluczowy dla efektywności systemu pneumatycznego. Kompresory tłokowe i śrubowe różnią się pod wieloma względami, co wpływa na ich zastosowanie w różnych warunkach. Kompresory tłokowe charakteryzują się prostą konstrukcją oraz niższymi kosztami zakupu i eksploatacji. Są one idealne do zastosowań, gdzie wymagane są krótkotrwałe dostawy sprężonego powietrza. Z kolei kompresory śrubowe są bardziej zaawansowane technologicznie i zapewniają ciągłą pracę przez dłuższy czas. Dzięki swojej konstrukcji są bardziej wydajne i cichsze, co czyni je idealnym rozwiązaniem dla przemysłu. Warto również zauważyć, że kompresory śrubowe mają większą żywotność i wymagają mniej konserwacji niż ich tłokowe odpowiedniki. Wybór między tymi dwoma typami powinien być uzależniony od specyficznych potrzeb użytkownika oraz warunków pracy.
Jakie są najważniejsze parametry techniczne kompresorów?
Przy wyborze oraz łączeniu kompresorów kluczowe jest zwrócenie uwagi na kilka istotnych parametrów technicznych, które mają wpływ na ich wydajność oraz funkcjonalność. Pierwszym z nich jest ciśnienie robocze, które określa maksymalną wartość ciśnienia, jakie może osiągnąć dany kompresor. Ważne jest, aby oba urządzenia miały podobne wartości ciśnienia roboczego, aby uniknąć problemów z równomiernym obciążeniem systemu. Kolejnym istotnym parametrem jest wydajność, mierzona w litrach na minutę lub metrach sześciennych na godzinę. Wydajność powinna być dostosowana do wymagań narzędzi pneumatycznych oraz innych urządzeń korzystających ze sprężonego powietrza. Dodatkowo warto zwrócić uwagę na pojemność zbiornika sprężonego powietrza – większy zbiornik pozwala na dłuższe użytkowanie narzędzi bez konieczności częstego uruchamiania kompresora.
Jakie są najlepsze praktyki dotyczące konserwacji kompresorów?
Aby zapewnić długą żywotność i efektywność działania kompresorów, niezwykle istotna jest regularna konserwacja tych urządzeń. Przede wszystkim należy systematycznie sprawdzać poziom oleju w kompresorach olejowych oraz wymieniać go zgodnie z zaleceniami producenta. Regularna wymiana filtrów powietrza to kolejny kluczowy element konserwacji – brudne filtry mogą ograniczać przepływ powietrza i wpływać na wydajność całego systemu. Warto także kontrolować stan uszczelek oraz złączek, aby uniknąć nieszczelności prowadzących do utraty ciśnienia. Oprócz tego zaleca się okresowe przeglądy techniczne przeprowadzane przez wykwalifikowany personel, który będzie mógł wykryć ewentualne usterki zanim staną się one poważnym problemem. Czyszczenie chłodnic oraz wentylatorów również ma znaczenie dla efektywności pracy kompresora – zanieczyszczone elementy mogą prowadzić do przegrzewania się urządzenia i jego awarii.
Jakie zastosowania mają połączone kompresory w przemyśle?
Połączone kompresory znajdują szerokie zastosowanie w różnych branżach przemysłowych, gdzie wymagane jest dostarczanie sprężonego powietrza do różnych procesów produkcyjnych lub usługowych. W przemyśle budowlanym połączone kompresory mogą zasilać narzędzia pneumatyczne takie jak młoty udarowe czy wiertarki, co znacznie zwiększa efektywność pracy ekip budowlanych. W zakładach produkcyjnych sprężone powietrze jest wykorzystywane do napędzania maszyn oraz automatyzacji procesów produkcyjnych – połączenie kilku kompresorów pozwala na zapewnienie ciągłego dostępu do sprężonego powietrza nawet przy dużych obciążeniach. W branży motoryzacyjnej połączone kompresory mogą być używane do lakierowania pojazdów czy obsługi narzędzi serwisowych. Dodatkowo w sektorze spożywczym sprężone powietrze znajduje zastosowanie w pakowaniu produktów oraz ich transportowaniu w zamkniętych systemach pneumatycznych.
Jakie są koszty związane z łączeniem dwóch kompresorów?
Koszty związane z łączeniem dwóch kompresorów mogą być różnorodne i zależą od wielu czynników takich jak typ wybranych urządzeń, materiały potrzebne do instalacji oraz ewentualne koszty robocizny związane z montażem systemu. Przede wszystkim należy uwzględnić cenę zakupu drugiego kompresora – koszt ten może się znacznie różnić w zależności od marki, modelu oraz jego parametrów technicznych. Dodatkowo konieczne będzie zakupienie odpowiednich akcesoriów takich jak rury, złączki czy uszczelki, co również wiąże się z dodatkowymi wydatkami. Jeśli planujemy samodzielny montaż systemu, warto uwzględnić także koszty narzędzi potrzebnych do wykonania pracy – niektóre z nich mogą być drogie lub wymagać wynajmu specjalistycznego sprzętu. Koszt robocizny to kolejny aspekt, który należy rozważyć – jeśli zdecydujemy się na zatrudnienie fachowców do wykonania instalacji, może to znacząco zwiększyć całkowity koszt przedsięwzięcia.
Jakie są najlepsze źródła informacji o kompresorach?
Aby uzyskać rzetelne informacje na temat kompresorów oraz ich łączenia, warto korzystać z różnych źródeł wiedzy. Przede wszystkim, dokumentacja producentów to kluczowy element, który dostarcza szczegółowych informacji na temat parametrów technicznych oraz zasad użytkowania konkretnych modeli. Warto także odwiedzać fora internetowe oraz grupy dyskusyjne, gdzie użytkownicy dzielą się swoimi doświadczeniami i poradami dotyczącymi kompresorów. Publikacje branżowe oraz artykuły naukowe mogą dostarczyć cennych informacji na temat nowinek technologicznych oraz trendów w branży pneumatycznej. Szkolenia oraz warsztaty organizowane przez producentów lub specjalistyczne firmy to kolejna doskonała okazja do poszerzenia wiedzy na temat kompresorów oraz ich zastosowań. Warto również korzystać z materiałów wideo dostępnych w Internecie, które pokazują praktyczne aspekty łączenia kompresorów oraz ich konserwacji.